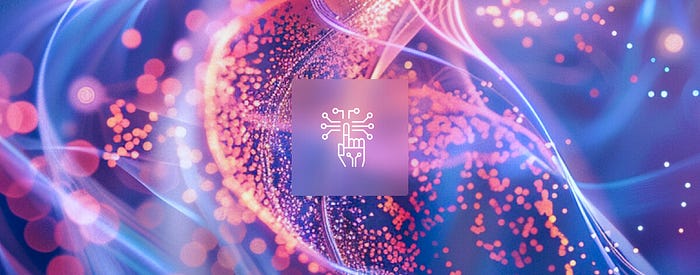
Imagine a factory not just humming with machinery, but pulsing with intelligence. This is the future promised by AI, which is rapidly transforming the landscape of production. At the heart of this change lies machine learning, an artificial intelligence subset that influences process optimization without explicit programming.
Fueled by vast datasets collected from sensors and interconnected machines, ML algorithms are revolutionizing factories’ workflows. The global market size for AI in the industry was $5 billion in 2023 and is expected to reach $68 billion by 2032. Predictive maintenance, for instance, leverages machine learning in manufacturing to analyze equipment data and anticipate failures before they occur, minimizing downtime and maximizing productivity. Additionally, these algorithms can identify patterns in production lines, pinpointing bottlenecks and suggesting adjustments for peak efficiency.

Employees today face a relentless drive for optimization. Consumers demand ever-evolving products at competitive prices, and global competition is fierce. AI offers a powerful weapon in this battle. By streamlining processes, improving quality control, and fostering data-driven decision-making, artificial intelligence empowers people to stay ahead of the curve. The future of Generative AI in manufacturing promises to be one of smart machines working alongside a skilled human workforce, crafting the products of tomorrow.
Today we’ll help you learn more about machine learning in manufacturing examples. If you feel like that’s what you’re looking for — this article is for you!
The Power of Machine Learning in Manufacturing
The role of predictive analytics nowadays is hard to overestimate. Machine learning development is revolutionizing manufacturing, with statistics painting a clear picture of its positive impact. Here’s how ML is transforming the industry:
- Boosting Productivity and Efficiency: Now more than 80% of companies and businesses need employees with machine learning skills. It’s essential for fewer equipment breakdowns, smoother production flow, and ultimately, a significant increase in output.
- Enhancing Product Excellence: Traditional quality control methods often have limitations. Machine learning, on the contrary, shines here. There is a significant reduction in defects with the algorithms analyzing vast amounts of data from sensors and cameras. This leads to fewer faulty products reaching consumers, saving workers money, and strengthening brand reputation.
- Minimizing Maintenance Costs: Unscheduled equipment failures can be crippling. Here, ML comes to the rescue. By analyzing sensor data, the algorithms can predict equipment breakdowns before they occur, allowing for proactive maintenance. This translates to lower repair costs and extended equipment lifespan.
The key to ML’s success lies in its ability to analyze massive datasets. They contain information on everything from sensor readings to creation line performance. The algorithms then identify patterns within this data, allowing them to predict future outcomes and optimize processes. For instance, machine learning can foresee when a specific machine is likely to fail, enabling employees to schedule maintenance before a breakdown disrupts output.
Predictive analytics is no longer a futuristic concept — it’s a powerful tool driving a smarter future for manufacturing. As data collection and algorithms continue to evolve, we can expect even greater advancements in efficiency, quality, and cost savings, solidifying industrial machine learning as a cornerstone.
Demystifying ML Benefits for Business: A Practical Approach
Picture a program that gets sharper with experience, like a seasoned athlete continually honing their skills. That’s the essence of machine learning. It’s a branch of artificial intelligence where algorithms are trained on information to identify patterns and make predictions.
Think of a manufacturer feeding data on past production cycles, equipment sensor readings, and product quality checks. By analyzing these vast datasets, the algorithm learns to recognize patterns.
But ML’s superpowers extend beyond equipment health. Imagine a camera system trained on millions of images of flawless products. The algorithm can then identify even the most minor defects in real time, leading to improved product quality. No more relying on human inspectors prone to fatigue or missing subtle flaws.

The real magic lies in data-driven decision-making. Machine learning analyzes information to pinpoint bottlenecks and inefficiencies. This reveals that a specific vehicle is causing delays. With this insight, workers can optimize production flow, reallocate resources, and plan output more effectively.
This is just the tip of the iceberg of machine learning use cases in manufacturing. From optimizing inventory control to personalizing product recommendations, Generative AI in supply chain management offers a treasure trove of possibilities. By embracing this technology, factories worldwide can unlock a future of smarter operations, improved efficiency, and a sharper competitive edge.
Leave a Reply